Customer Purchased Parts
Scenario: Andy and Jan want to save money on their new dream home so they decide to purchase factory-second doors from a cut-rate supplier. However, from my experience, customer purchased materials can result in a real dilemma for a contractor and themselves as homeowners. Here’s why…
Every customer wants to save money on parts, and they want the best quality for the lowest price. Most customers believe that contractors unreasonably mark up materials. What I do is provide the best quality parts at a reasonable price, whether that means doors, windows, roofing material, concrete, flooring, siding, plumbing fixtures, and so on. Maybe the homeowner wants to buy concrete from the supplier because the contractor can make money on that transaction. This middleman work is actually a substantial part of being a contractor: providing the segments that build a house, and in most cases, a dream home. What the homeowner often doesn’t see included in that purchasing matter is, first, the critical point of timeliness. When the homeowner purchased materials are not on site at the proper time, it delays the project which, in turn, costs the homeowner in the long run. Second, if the materials are on site too early, I have to pay my team to protect the product until it’s ready to use. Third, as a contractor I stand behind the materials because all of my suppliers give me products that I can guarantee. In the long run, the time factor and warrantee saves the homeowner money.
In delving further, homeowners typically go to a cut-rate supplier or big box store and buy materials that are not right for the project and/or do not match the building plans. The most common issue from my experience has been customer purchased doors. I don’t mind them picking them out; that’s the idea of building what they want. But the best case hassle-free scenario is to allow the contractor to supply those doors. Most of the time, in the long run, the old saying ‘you get what you pay for’ comes true in the building world.
For example, a customer bought their own doors that were two inches taller than what the plans called for. He might have saved $500 on the doors, but it cost them $1000 to reframe every opening for each door to make them fit, so he didn’t save any money. Normally I invest two man hours installing a front entryway door and one man hour for each other door. We spent seven man hours doing one front entry door and it still has issues because the door is warped.
Buying “seconds” entails homebuilding materials that are just that, seconds. There’s a reason why these homebuilding parts are at cut-rate suppliers. They were sent from the manufacturer because they didn’t make the standard grade. It’s a factory second. That’s what they distribute. It’s not unlike an outlet where you can buy irregular items. They look beautiful and often cheaper but there’s still something innately flawed. Maybe the product is not square, or it’s warped. These cut-rate outlets may also have first-rate products, but the price will reflect that quality grade.
Plumbing fixtures are another typical homeowner “saving” purchase. Many times customers will go to Home Depot and get a plumbing fixture – just like the one my plumber showed them – but it’s 40% cheaper. The plumber may mark the fixture up by 10% but he’s also selling quality products he can guarantee, so there is a reason for marked up goods in the contractor world. Usually, my plumber can’t obtain parts for some fixtures because they are solely made for Lowe’s, Home Depot or other big box stores. Home Depot is a big box store like WalMart; they dictate to Moen and Kohler what they will pay for a product. For example, Moen makes cheaper Chinese-outsourced plumbing products. It still has their name on it but it’s a line only made for Home Depot or Lowe’s. It’s not Moen’s standard line and it doesn’t have the same quality standard parts in them. They do make a standard grade that they sell to plumbers and retail outlets, such as Haney’s or Ferguson’s. Home Depot and big box stores sell the inferior look-alike product but it’s a cheaper grade. My plumber has to go through China to get such non-standard parts, and by the time he gets an O-ring or plastic compression fitting that’s a special size, the job’s not cost-effective any more. Furthermore, if a customer purchased fixture starts leaking six months later, there’s no guarantee. The plumber’s going to charge $80 an hour to fix that because he did not supply that part.
WalMart paint is another contractor nightmare. If you’ve purchased and used WalMart paint, you too have experienced its incongruence with the market’s paint standards. A job with WalMart paint may take five coats to cover a surface and still not qualify for the kind of standard that I provide and guarantee. Years ago, we built a house for a customer who was on a very tight budget. We built a beautiful home as inexpensively as possible. She decided to do the painting to save herself some money. A year or two later, she asked me to come back and do a tile entry at the front door. When I first went to her house, I couldn’t believe the chaotic paint job in the front entryway and living room; every line from the roller could be seen going every which way. It was the worst paint job I had ever seen. After building a quality home, I thought every time she invites somebody over and they walk in the front door, they may go, ‘Oh! Who built your house?’ and my name’s all over that paint job. They may not notice that the corners are perfectly square or how solid the floors are in the kitchen and living room, that the siding is jointed flawlessly, that every joint of the trim is perfectly mitered, and so on. I felt so bad about my reputation because observers may think we did the painting. I felt like sending a painting crew over, pay out of my pocket just to erase the WalMart “paint” job and make it match the excellence of the rest of her new residence, just to verify my name-stamp on the home.
In conclusion, from my experience of customer purchased materials, not many of them have worked out suitably. Overall, they have been across-the-board nightmares and have ended up costing the customer more time and money, so I am recommending homeowners to think twice about purchasing their own homebuilding parts and to work with the contractor before they try to “save money.” It’s frustrating as a contractor to provide 90% of a house. On the contrary, when a customer allows the contractor to provide all of the homebuilding materials – with the choice options open for styles and the customer’s likes – the home gets built in time complete with guaranteed parts and fixtures, whether that be electrical, plumbing, roofing, painting, the works. The project stays on schedule and on budget, along with providing the end-product, your new home, which we stand behind.
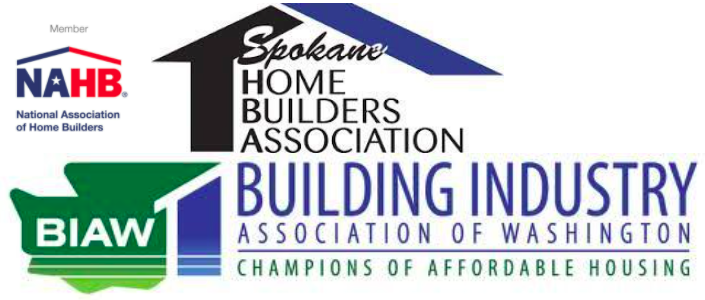